Thermal power plants are crucial for electricity generation due to their reliability and ability to provide a continuous and stable power supply. They play this pivotal role by harnessing fossil fuels such as coal or natural gas to generate electricity. Consequently, fossil fuel-based thermal power plants face environmental challenges as they release greenhouse gases and other pollutants.
Operating with a streamlined approach, thermal power plants can significantly curtail carbon emissions by optimising its fuel consumption, ensuring that less fuel is employed to produce an equivalent amount of electricity. In essence, efficiency becomes the cornerstone, allowing these thermal power plants to make a substantial impact on reducing their carbon footprint, while reducing operating cost, in an effective manner.
Sultan Azlan Shah Power Station
Jimah East Power Station
The efficiency of a thermal power plant, whether it's a Combined Cycle Gas Turbine (CCGT) or an Ultra-Supercritical Coal (USC) Plant1, is typically measured using a parameter called "heat rate" or "thermal efficiency." The heat rate is a measure of how efficiently the power plant converts the energy from its fuel into electricity. Heat rate is expressed in units of energy input per unit of electrical output and is usually measured in joules per kilowatt-hour (GJ/KWh). A lower heat rate indicates a more efficient power plant because it means that less fuel is required to produce each unit of electricity. In TNB, heat rate or thermal efficiency is one of the key indicators that are continuously monitored throughout the life of the thermal power plant.
Plant Operational Efficiency Enhancements
Power plants encounter various challenges in their efforts to sustain and improve their operating efficiency. Some common challenges include operational wear and tear due to continuous long hours of operation, aging Infrastructure where older power plants may have outdated equipment and technology, making it challenging to achieve and maintain high levels of optimal efficiency. In addition, inconsistent fuel quality or interruptions in fuel supply can lead to suboptimal performance and reduce overall efficiency.
Power plant efficiency is also contributed by effective monitoring of power plant auxiliary consumption. Power plant auxiliary consumption refers to the energy used by various support systems and equipment within the power plant that are necessary for its operation but do not directly generate electricity. While the goal is to keep this consumption as low as possible to maximize the amount of electricity the plant can provide to the grid, some auxiliary consumption is necessary for the plant to work properly. Nevertheless, reducing auxiliary consumption is a straightforward method to improve plant efficiency and lower carbon emissions because it means the power plant doesn't have to burn additional fuel to generate extra electricity for the grid.
At TNB, we continue to monitor and implement initiatives to improve thermal power plant efficiency. Our aim is to improve plant efficiency to its design level. Some of these initiatives include:
1. Initiatives to improve overall power plant efficiency
- Ensure optimum coal fineness for different types of coal characteristics to improve boiler efficiency and combustion stoichiometry
- Water-wash Air Pre-Heater (APH) element basket during annual short outages and complete replacement during major overhaul.
- Carry out condenser cleaning during plant outage to improve condenser vacuum.
- Set up Efficiency Improvement Team (EIT) to closely monitor, analyze and execute plant technical efficiency improvement works.
- Enhance remote monitoring of plant efficiency using advanced digital technology and artificial intelligence such as Digital Twin and PI Vision.
- Install zero leakage valve and thermography equipment to identify passing valve to improve water steam cycle.
about power plant operations
Waste not! The air pre-heater (APH) reuses heat from the flue gas (that would have otherwise been wasted) to pre-heat combustion air for the boiler. Thus, less energy is required to heat the boiler to its design temperature, increasing the boiler’s thermal efficiency.
2. Initiatives to improve power plant auxiliary consumption
- Co-fire coal of high sulfur content with lower sulfur brands to reduce auxiliary consumption on FGD Aeration Fan & FGD Absorber Spray Pump
- Install check valve at Boiler Sum Pump.
- Optimise air compressor auto-changeover frequency
- Optimise operation of Main Cooling Water pump (CWP) based on dispatchable load condition of main plant.
- Optimise voltage setting for Electrostatic Precipitator (ESP) transformer to improve particulate removal prior to emissive discharge.
- Install zero leakage valve and thermography equipment to identify passing valve to improve water steam cycle.
about power plant operations
FGD stands for flue gas desulfurization.
The check valve installed at the boiler sump pit prevents water from the discharge pipe to backflow to the sump pit. Backflow water increases the water level in the sump pit, causing the pump to run more frequently thus increasing auxiliary consumption.
ESP – Electrostatic Precipitator – helps with pollution control by removing fine particulate matter, like ash, dust, and soot from exhaust fumes.
Impactful Initiatives: Emission Reduction
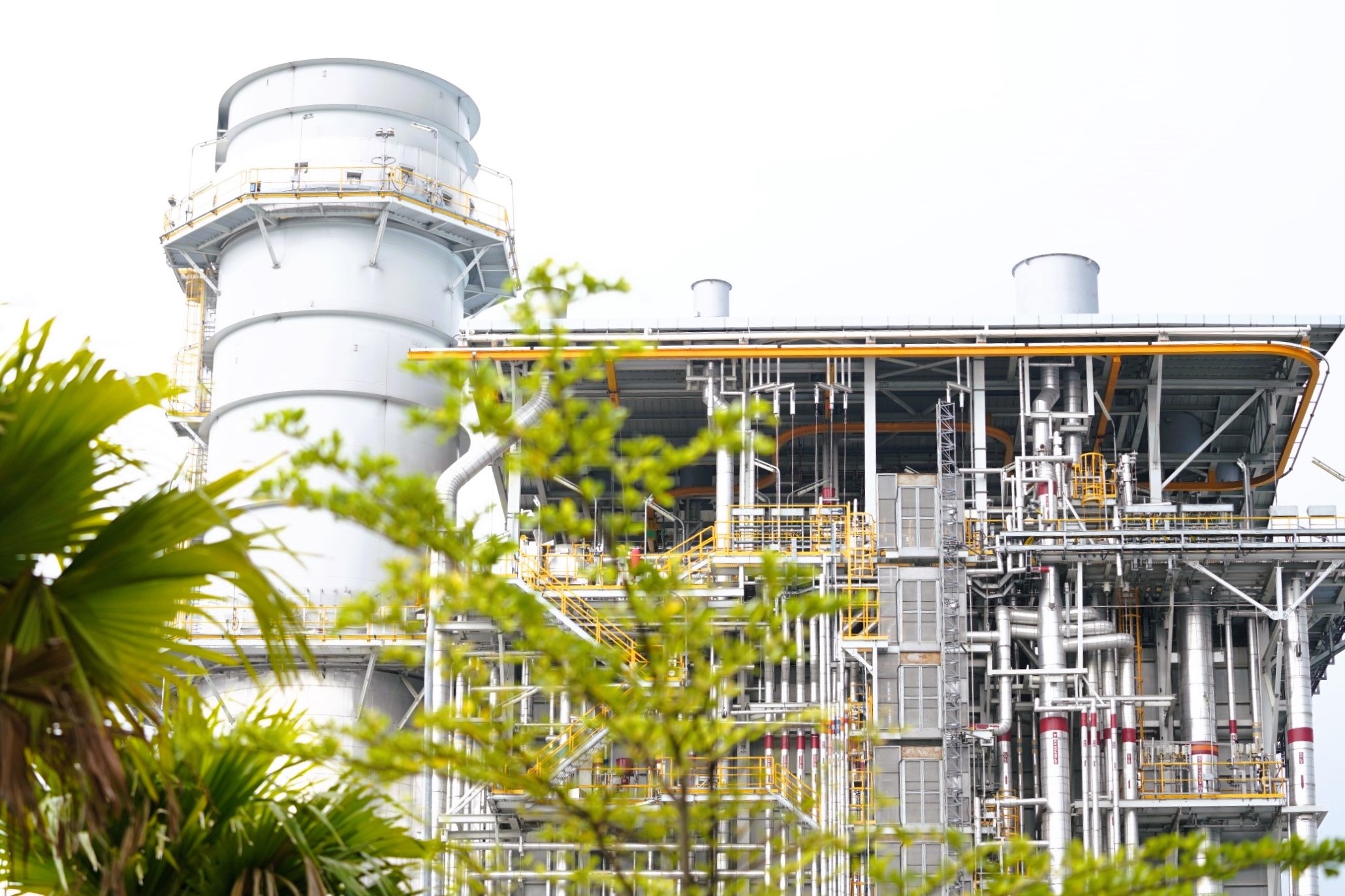
Our efforts have produced a commendable enhancement of the heat rate efficiency of thermal power plants in the TNB portfolio, registering an improvement of +1.12% from 2022 to 2023 (FY2022: 9067 kJ/KWh, FY2023 as of September: 8,965 kJ/KWh).
The resulting carbon emission reduction is 301,538.07 tCO2e (equivalent to carbon sequestered by 4,985,957 tree seedlings grown for 10 years)2.
With myTNB mobile app, customers with smart meter are further empowered to embrace an energy-efficient lifestyle through interactive energy usage alerts, specifically through the Energy Budget feature. This innovative tool is part of a suite of digital solutions designed to guide customers toward a more sustainable and energy-efficient way of living.
Note 1: the ultra-supercritical (USC) technology is an efficient coal-burning technology with a 40% efficiency as against conventional coal-fired power plant which has 36% efficiency. At TNB, Jimah East Power, Manjung 4 & Manjung 5 employ USC technology.
Note 2: as calculated using US EPA greenhouse gas equivalent calculator https://www.epa.gov/energy/greenhouse-gas-equivalencies-calculator