Tenaga Nasional Berhad (TNB), as a utility company with substantial water usage in power generation, we recognize our responsibility to manage this vital resource in a sustainable manner.
Despite the withdrawal of water from seawater, surface water and town water for our operations, 99.9% of the water withdrawal is discharged back to the respective sources. Therefore, our focus in managing water withdrawal is on optimizing the use of the 0.1% town water withdrawal, which is mainly used in power generation operated by TNB Genco, a wholly-owned subsidiary of TNB. By treating the wastewater, 0.013% of the 0.1% of town water we withdraw is safely discharged back into nature. Thus, the main efforts are concentrated on optimizing the use of the remaining town water withdrawal through operational excellence, technologies, and innovation.
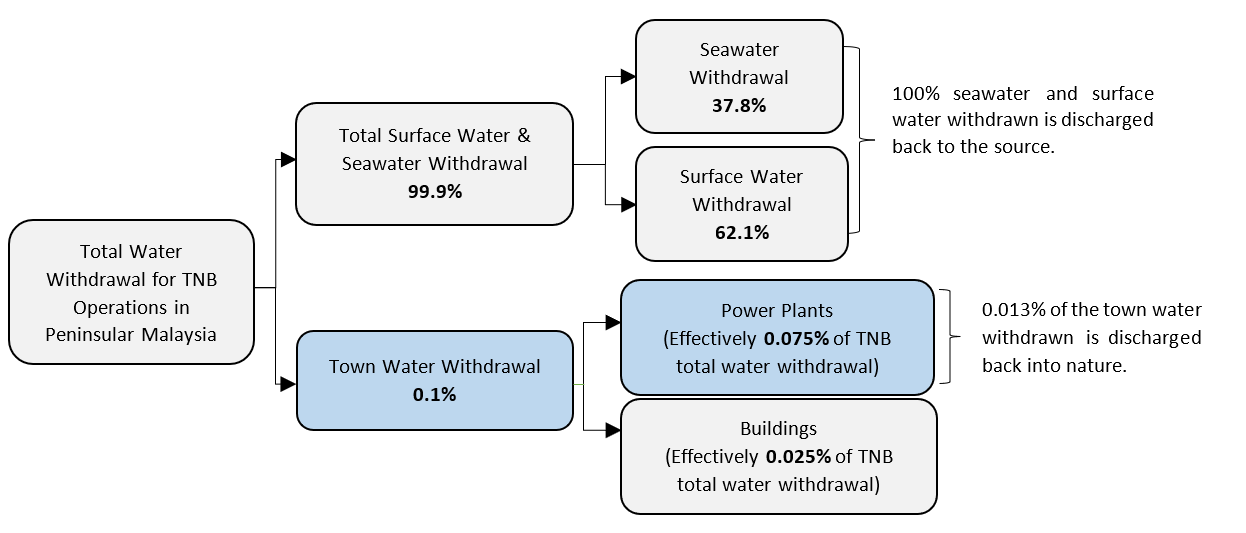
Note: The diagram above includes Hydro Power Plant
Closed-Loop Steam Generation Process Helps to Optimize the Use of Town Water Withdrawal
As pioneers of 'Combine Cycle Gas Turbine' and 'Ultra Super Critical Boiler' technology in South-East Asia, we are dedicated to operational excellence. Water consumption plays a pivotal role in our steam generation process and operational efficiency, designed as closed-loop system aimed at minimising our reliance on town water sources. While make-up water is only needed to cover any losses due to blowdown or vent in maintaining water quality. This system is crucial for sustainable operations as it significantly reduces our water withdrawal from town water.
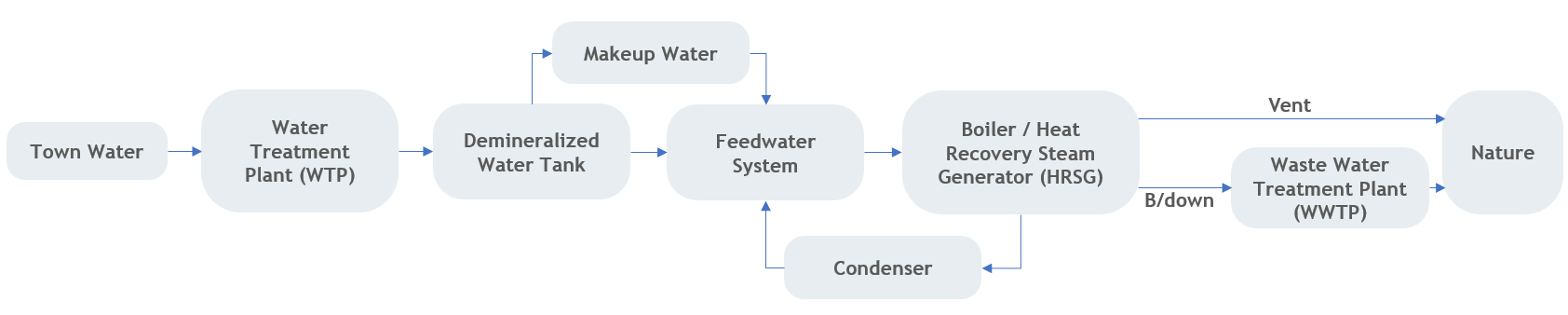
Simplified process of feedwater for steam generation
Effective management of makeup water and blowdown is paramount for ensuring optimal boiler performance, overall power plant efficiency, and safety. The careful control and quality assurance of makeup water are fundamental; any inadequacy or impurity in this supply may not only compromise efficiency but also pose significant safety hazards within our operations.
From 2023 to date, average Water Intensity (water consumption from town water source per net generation of respective plant) for our power plants are much lower than our counterparts using similar power plants technology. This is illustrated in the following table:
TNB Genco Thermal Power Plant Water Consumption Intensity1 | ||||
---|---|---|---|---|
No | TNB Genco Thermal Power Plant | Water Intensity, Liter/kWh | Steam-water Cycle | |
TNB Genco Thermal Power Plants (Year 2023) | International Counterparts2 | |||
1 | TNB Janamanjung 1,2,3(JMJG GF1), TNB Manjung 4 (M4) & TNB Manjung 5 (M5) | 0.161 |
0.36 – 0.52 (Ultra Super Critical Boiler |
Closed-Loop |
2 | Jimah East Power (JEP) | 0.097 | Closed-Loop | |
3 | Kapar Energy Ventures (KEV) | 0.242 |
.41 – 0.57 (Sub-Critical Boiler) |
Closed-Loop |
4 | Connaught Bridge Power Station (CBSB) | 0.062 |
0.27 – 0.45 (CCGT) |
Closed-Loop |
5 | Gelugor Power Station (SJ GLGR) | 0.034 | Closed-Loop | |
6 | Prai Power Station (TNB Prai) | 0.010 | Closed-Loop | |
7 | Tuanku Jaafar Power Station (TJPS) | 0.068 | Closed-Loop | |
8 | Sultan Ibrahim Power Plant (SPG) | 0.072 | Closed-Loop |
Table comparison of power plant water consumption intensity of TNB Genco Thermal Power Plants and International Counterparts
TNB Genco Thermal Power Plants Located at Low Water Stress Area
All our coal and combined cycle power plants are located in areas with low water stress, none of them are located in the water stress area, therefore zero (0) water withdrawals from water-stressed regions. This strategic placement highlights our commitment to sustainable resource usage and community harmony, preventing potential conflicts over water resources between industry and local communities. The process begins from planning and construction of the respective thermal power plants.
In addition, all of our coal and combined cycle power plants were built and continue to operate in accordance with global “World Bank Environmental and Social Standards” which were established based on the initial project bidding requirements. These standards include water consumption process which are archetypical of conventional high-efficiency thermal plants. Additional efforts at the operational level illustrate our commitment and unwavering dedication to responsible resource management underscoring our proactive efforts in fostering sustainability within our operations.
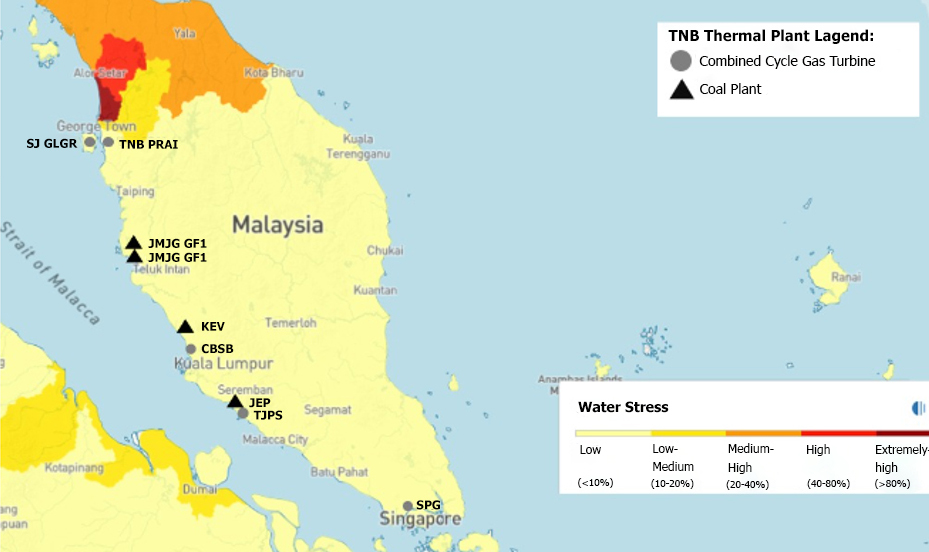
Water Stress Mapping based on Aqueduct by World Resources Institute and location of TNB Genco Thermal Power Plants
Alternative Water Sources for Power Plant Cooling System
Water plays a dual role in our plant operation, serving not only as a vital element in steam generation but also as a crucial component within our cooling systems. To reduce our dependence on town water sources, we implement alternative sources such as seawater or river water, effectively reducing our reliance on town water.
No | TNB Genco Thermal Power Plant | Capacity | Water source for cooling system |
---|---|---|---|
1 | TNB Janamanjung 1,2,3 (JMJG GF1) | 2,070MW | Seawater |
2 | Kapar Energy Ventures (KEV) | 2,100MW | |
3 | TNB Manjung 4 (M4) | 1,010MW | |
4 | TNB Manjung 5 (M5) | 1,000MW | |
5 | Jimah East Power (JEP) | 2,000MW | |
6 | Prai Power Station (TNB Prai) | 1,000MW | |
7 | Tuanku Jaafar Power Station (TJPS) | 1,411MW | |
8 | Sultan Ibrahim Power Plant (SPG) | 1,440MW | |
9 | Connaught Bridge Power Station (CBSB) | 375MW | River Water |
10 | Gelugor Power Station (SJ GLGR) | 310MW | Not applicable (Air cooled) |
Water source for cooling system 2023
Our cooling process, facilitated through the open circuit Main Cooling Water (MCW) system, operates efficiently by utilizing seawater or river water and subsequently discharging it back into the sea at the allowable discharge temperature and free chlorine level that meet DOE Standard. This ensures zero net water consumption, exemplifying our commitment to sustainable practices by minimizing environmental impact while maintaining operational efficiency. Our approach adheres to global water conservation standards set forth by Electric Power Research Institute (EPRI).
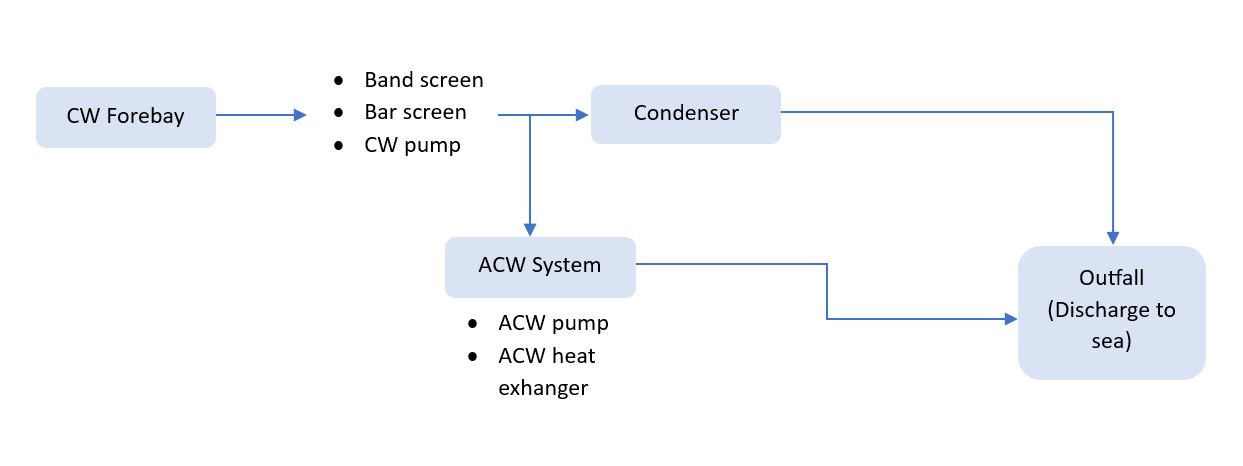
Simplified process of Main Cooling Water (MCW) system
Rainwater Harvesting as Alternative Water Source for Coal Yard Dust Suppression System
At TNB Janamanjung and Jimah East Power, rainwater is harvested as an alternative water source for the coal yard dust suppression system, reducing reliance on town water. The collected rainwater is stored in a pond before being directed to the water process tank for dust suppression. This initiative helps optimize the use of town water in our power plant operations.
The capacity of rainwater ponds are as below:
No | Rainwater Pond Location | Storage Capacity |
---|---|---|
1 | TNB Janamanjung | 1,375m3 |
2 | Jimah East Power | 1,890m3 |
The rainwater ponds allow the collection and reuse of rainwater, thus further helping to reduce the environmental footprint of our generation sites.
Driving Innovation for Sustainable Operations
Through our proactive 'Operational Excellence' best practices and 'Business Turnaround Program' initiated in 2017, we persistently monitor and execute water conservation initiatives within power plant operations. Our comprehensive methodology allows us to meticulously identify, plan, and implement impactful strategies for conserving water resources. Furthermore, we specialize in state-of-the-art reverse engineering and plant upgrade initiatives, aligning with our dedication to achieve world-class operational performance in power plants. For instance, one or our Combined Cycle Gas Turbine (CCGT) plant which is Sultan Ibrahim Power Plant (SPG) has experienced an increasing trend in water consumption intensity from 2021 to the present. From 2021, a steady increase of water consumption intensity has been recorded rising from 0.02 Liter/kWh to 0.08 Liter/kWh. Although this remains lower than the average international counterparts in United State which range from of 0.27 to 0.45 Liter/kWh2, we are committed to further reduce town water consumption. To address this, we plan to install 100 units of Zero Leakage Valve at the Heat Recovery Steam Generator (HRSG) of SPG plant during plant maintenance inspection in August 2024. This exemplifies our ongoing commitment to sustainable operations and continuous improvement.
Role of TNB Sustainability and Energy Transition Committee (SETC) for Water Management Strategy and Performance
The TNB Sustainability and Energy Transition Committee (SETC) is chaired by the President/Chief Executive Officer (CEO) comprising TNB Top Management Team, to ensure executive-level responsibility for environment, social and governance (ESG) matters. TNB SETC plays the role of steering the development of sustainability and energy transition strategies and policies, and its implementation as well as providing oversight and input on opportunities and risk exposures.
At TNB, we recognize that water is a finite resource. Water management initiatives and performance are among the key focus areas that are presented and deliberated in the SETC, demonstrating our commitment to efficient water management in our operations. Our commitment to water efficiency is not just a responsibility but also a testament to our dedication to sustainable practices and resource conservation.
Note
1 – Water consumption based on municipal/ town water consumption
2 – Average international counterparts water consumption intensity of United State depicted from report of “A Review of Operational Water Consumption and Withdrawal Factors for Electricity Generating Technologies in the United States” (March 2011) by NREL is a national laboratory of the U.S. Department of Energy, Office of Energy Efficiency & Renewable Energy, operated by the Alliance for Sustainable Energy, LLC
Plant Technology | Water Consumption Factor or Intensity | |
Gallons/MWh | Liter/kWh (after conversion) | |
Coal Subcritical | 90 – 125 | 0.41 – 0.57 |
Coal Supercritical | 80 – 115 | 0.36 – 0.52 |
Natural Gas Combined Cycle | 60 – 100 | 0.27 – 0.45 |